Подшипники турбогенераторов
К подшипникам турбогенератора предъявляются очень высокие требования в смысле надежности и долговечности их работы, малых потерь на трение и возможной точности установки. Срабатывание подшипника может привести к серьезной аварии (особенно у реактивных турбин), а неточность установки вызывает вибрацию турбины.
Исследования условий работы подшипников привели к следующим выводам:
-
Во время нормальной работы между шейкой вала и вкладышем всегда должен быть зазор, заполненный слоем масла, исключающий возможность соприкосновения металла с металлом.
-
Это условие лучше всего осуществляется, если между шейкой вала и вкладышем есть зазор, суживающийся в направлении вращения вала (клиновидный зазор); наиболее узкое место зазора должно быть внизу шейки недалеко от места, где давление на вкладыш достигает самой большой величины. При такой форме зазора масло захватывается шейкой и загоняется в узкую часть зазора, где давление масла получается повышенным.
Причину этого нетрудно понять из следующего рассуждения.
Допустим, что диаметр расточки вкладыша несколько больше диаметра шейки вала. Тогда в спокойном состоянии шейка вала займет во вкладыше положение, схематически изображенное на (рис. 31а), причем шейка вала будет соприкасаться с внутренней поверхностью (баббитовой заливкой) нижней части вкладыша. Даже если мы введем во вкладыш масло, то этот металлический контакт сохраниться, так как масло будет выдавлено в том месте, где давление шейки на вкладыш достигает наибольшей величины.
С того момента как вал начнет вращаться, картина измениться. Вначале вал начнет как бы накатываться на вкладыш, двигаясь вправо. Когда усилие станет недостаточным для дальнейшего приподнимания вала при накатывании его на вкладыш, вал начнет вращаться относительно вкладыша, скользя по правой нижней его части. Благодаря своей вязкости масло будет налипать на шейку и увлекаться ею в зазор между вкладышем и шейкой.
Зазор тоже будет суживаться книзу, а давление масла в нем возрастать, причем максимальной величины оно достигнет перед самой узкой частью зазора. Вследствие разности давления масла в разных точках зазора вал всплывает на масляном слое, переместиться влево и займет положение, показанное на (рис. 31б). Толщина масляного слоя будет тем больше, чем выше число оборотов вала и вязкость масла.
Если просверлить в различных точках вкладыша отверстия и, присоединив к ним манометры, измерить давление масла в этих точках, то, откладывая в радиальных направлениях отрезки, соответствующие в определенном масштабе (например, 1 ата= 1 мм) величинам давлений в этих точках, мы получим кривую, подобную изображенной на (рис. 31в). Как видно из этой кривой, давление в клиновидном зазоре постепенно возрастает по мере его сужения, но достигает наибольшей величины (до 10-30 ати) не в самом узком месте зазора, а несколько ранее, и в расширяющейся части зазора становится близким атмосферному давлению.
Таким образом, при правильной расточке вкладыша трение металла о металл имеет место только при первых оборотах вала. Для уменьшения потерь на трение в это время вкладыш снабжен заливкой антифрикционным сплавом - баббитом. С того же момента, когда создается непрерывный масляный слой, материал заливки вкладыша по существу уже не имеет никакого значения с точки зрения потерь на трение.
Различают два типа расточки вкладышей опорных подшипников: цилиндрическая расточка и овальная ("лимонная") расточка.
Цилиндрическая расточка обычно употребляется для валов с диаметром меньше 200 мм и приводится по диаметру, равному диаметру шейки плюс величина верхнего зазора (при неподвижном состоянии вала), который принимают около 0,002 от диаметра шейки. При этом боковые зазоры будут меньше верхнего. Так, при шейке, равной 200 мм верхний зазор будет 200*0,002=0,4 мм, а боковые - по 0,2 мм.
Для валов большого диаметра мощных современных турбин чаще применяют "лимонную" расточку, при которой верхний зазор выбирают около 0,001 от диаметра шейки, а боковые зазоры - по 0,002 от диаметра шейки. Для того чтобы получить такие зазоры, вкладыш растачивают с прокладкой, удаляемой после расточки. Толщина прокладки берется равной сумме верхнего и бокового зазоров. Диаметр расточки равен диаметру шейки вала плюс сумма боковых зазоров.
Если этот тип расточки принят для вала небольшого диаметра (60-100 мм),то абсолютная величина верхнего зазора не должна быть меньше 0,1 мм, а боковых зазоров - меньше 0,2 мм.
Точная величина зазоров в подшипник должна быть указана заводом изготовителем турбины, но ориентировочно можно пользоваться данными, приведенными выше или указанными на (рис. 32).
- Крестообразные канавки для масла в нижнем вкладыше недопустимы, как понижающие давление масла; еще хуже сквозные продольные канавки в нижней части этого вкладыша, несущей наибольшую нагрузку. Правильно выполненный подшипник вообще не должен иметь в нижней части вкладыша канавок.
Это обстоятельство нетрудно уяснить себе из (рис. 31г), где изображена примерная кривая давлений масла во вкладыше с канавкой в нижней части. В этом случае давление возрастает нормальным образом в направлении вращения до канавки. В канавке, если она доведена до краев вкладыша, давление падает примерно до атмосферного. В соответствии с этим шейка вала устанавливается ниже, чем на (рис. 31в), что вызывает уменьшение зазора слева от канавки, где давление вновь возрастает. Минимальный зазор между шейкой и вкладышем будет в этом случае меньше, чем при отсутствии канавки, а следовательно, масляный слой будет тоньше. Такой подшипник будет менее надежен в работе, так как появиться опасность нарушения непрерывности маслянного слоя, например, при вибрациях вала.
-
Смазывающие свойства масла ухудшаются при его нагревании; предельной безопасной температурой масла в подшипниках нужно считать 70о С, так как при температурах выше 70о С начинается интенсивное окисление масла. С другой стороны, и слишком низкая температура, увеличивая вязкость масла, неблагоприятно отражается на работе подшипников.
Температура масла, поступающего на подшипники, не должна быть ниже 35о С и выше 45о С.
При выполнении указанных условий, правильной установке подшипников и хорошем качестве масла изнашивание вкладышей совершенно ничтожно; после непрерывной многолетней работы турбогенератора часто сохраняются легкие следы резца на вкладыше, оставшиеся при его первоначальной расточке.
Подшипники турбогенератора можно разделить на две основные группы:
- опорные подшипники;
- упорные подшипники.
Опорные подшипники.
Опорные подшипники могут быть жесткими (цилиндрическими) и самоустанавливающимися (с шаровой опорой).
Жесткий опорный подшипник состоит из вкладыша (рис. 33), крышки и стойки (стула), отлитой заодно с корпусом турбины или же прикрепленной болтами к корпусу или фундаментной плите.
Вкладыши отливают из стали или высококачественного чугуна и с внутренней стороны заливают баббитом. У нас принят баббит марки Б-83 следующего состава:
Олово | Сурьма | Медь | Свинец |
83% | 11% | 6% | - |
Общее количество примесей в баббите Б-83 не должно превышать 0,55%, свинца может быть до 0,35%.
Перед заливкой вкладыш нужно тщательно, до блеска, отчистить и облудить оловом. Баббит расплавляют и нагревают до 440о С, а заливаемую половину вкладыша - до 250о С. Заливка должна быть выполнена быстро, в один прием, непрерывной струей в вертикально поставленный вкладыш. При заливке оставляют большую прибыль, которую удаляют, когда металл окончательно затвердеет.
Наилучшие результаты дает центробежная заливка, при которой расплавленный баббит заливают во вращающийся на станке вкладыш. Центробежная сила отбрасывает и прижимает баббит к поверхности вкладыша, что дает очень плотный и ровный слой, который можно выполнить с минимальным припуском на обточку. Таким образом, этот способ дает, кроме высокого качества заливки, существенную экономию баббита.
Шейка должна прилегать к нижней половине вкладыша по дуге 60о (рис. 32); эта поверхность точно пригоняется шабровокой. По краям вкладыша делаются скругления или небольшие скосы шириной 10 - 20 мм и глубиной до 0,03 мм, показанные на (рис. 32), они служат для уменьшения скорости выхода масла и спокойного стекания его из вкладыша; их наличие уменьшает возможность растекания масла по валу. Нередко для этого делаются специальные проточки (круговые канавки) недалеко от концов вкладыша или устанавливаются маслоуловительные кольца.
На (рис. 34) показана конструкция опорного подшипника турбин ЛМЗ. Вкладыш состоит из двух чугунных частей - верхней 1 и нижней 2, залитых баббитом 3. По окружности вкладыш имеет подушки (опорные колодки) 4, привернутые винтами. Назначение этих колодок - дать возможность изменять положение вала при центровке турбины, что достигается изменением толщины прокладок 5, проложенных под колодками. Масло подается к вкладышу через отверстие 6; стенки отверстия тоже залиты баббитом во избежание отслаивания баббита вследствие проникновения масла, поступающего под давлением 1,5 ата, между баббитовой заливкой и телом вкладыша. Количество поступающего масла регулируется установкой диафрагмы 7, отверстие в которой подбирается таким, чтобы температура всех подшипников турбогенератора была одинакова. Из полости 8 идет канавка, подводящая масло к соединительной муфте на валу турбины (изображенный на (рис. 34) подшипник расположен с стороны низкого давления).
Масло уходит из вкладыша через отверстие 10, стекая к нему по кольцевой выточке 11. Для того чтобы масляная пыль не выбивалась наружу, между корпусом подшипника и вкладышами установлены маслозащитные кольца, состоящие каждое из четырех сегментов, отжимаемых наружу пружинками 13. Половинки вкладыша стянуты болтами 14.
Стыки крышек подшипников смазываются для непроницаемости спиртовым раствором шеллака или бакелитовым лаком. Свинцовую проволоку, зеленое мыло и другие материалы, могущие способствовать порче масла, применять не следует.
Самоустанавливающиеся подшипники имеют то преимущество, что как при опускании ротора турбины на них во время монтажа, так и во время работы они несколько поворачиваются на своих шаровых опорах в соответствии с прогибом вала и располагаются параллельно его шейкам; таким образом, зазоры по всей длине вкладыша получаются одинаковыми.
Упорные подшипники
Упорные подшипники имеют своим назначением обеспечивать определенное взаимное положение ротора турбины относительно статора в осевом направлении и воспринимать осевое давление ротора, не допуская его перемещений в осевом направлении. Рассмотрим два типа упорных подшипников: гребенчатый и сегментный.
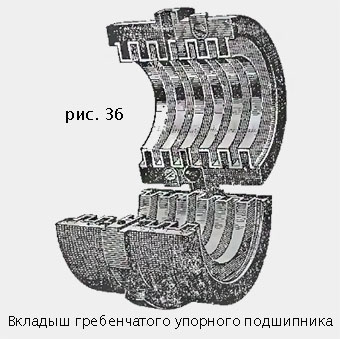
Гребенчатый подшипник (рис. 36) выходит постепенно из употребления; его устанавливали у активных турбин, осевое давление у которых вообще невелико, и у реактивных турбин небольшой мощности. Достоинством его является простота конструкции, недостатком - довольно большие потери на трение и большая длина, в особенности при значительной мощности турбины.
Гребенчатый подшипник обычно помещают на переднем конце турбины, иногда выполняя его в общем вкладыше с опорным подшипником .
При установке гребенчатого подшипника должна быть предусмотрена возможность игры (разбег) вала около 0,5 мм в осевом направлении.
Сегментный упорный подшипник, часто называемый "подшипник Митчелла", нашел значительное распространение на современных турбинах и с теми или иными конструктивными изменениями устанавливается почти всеми турбостроительными заводами. В конструкции его использован принцип, о котором мы уже упоминали, а именно, подвижная и неподвижная поверхности должны образовывать суживающийся в направлении движения вала зазор (клин).
В упорном подшипнике это условие можно соблюсти, разделив вкладыш на несколько отдельных сегментов, каждый из которых устанавливается под небольшим углом к поверхности движущейся части.
Общий вид сегментного подшипника в разобранном виде показан на (рис.39). Подшипник состоит из разделенного на две половины чугунного или стального вклаыыша (1 и 2) внутри которого помещаются две упорные шайбы: неподвижная 3 и жестко сидящая на валу 4. Между шайбами расположен ряд бронзовых колодок (сегментов) 5, залитых с рабочей стороны тонким слоем баббита.
В некотрых новых конструкциях подшипников сегменты выполняются из антифрикционной бронзы без заливки баббитом.
Действие сегментов нетрудно уяснить себе из (рис. 40); каждый сегмент 1 имеет на тыльной стороне эксцентрично помещенное ребро 2, около которого он может слегка повертываться. Благодаря этому сегмент при вращении упорной шайбы (гребня) 3 в направлении стрелки автоматически устанавливается в положение, наиболее благоприятное для образования клиновидного зазора, куда при вращении затягивается масло.
От расположения опорного ребра сегмента по радиусу (рис. 40) теперь часто отказываются и, например, ЛМЗ располагает ребро согласно (рис. 41) то есть не радиально, а параллельно выходной кромке сегмента; это приводит к одинаковому зазору по длине выходной кромки. Иногда, имея ввиду большие скорости масла на большем радиусе, ребро качения наклоняют еще сильнее так, что щелевой зазор на выходной кромке сегмента получается на внешнем радиусе больше, чем на внутреннем. Такое изменение в расположении опорного ребра должно способствовать более равномерному распределению давления масла и увеличивать несущую способность подшипника; одновременно уменьшается возможность наблюдающейся иногда выработки верхней части выходной кромки сегментов.
Нередко сегменты опираются не на ребра, а на уступы, штифты и шарики.
Для того чтобы сегменты не вращались вмести с упорным гребнем вала, на неподвижной шайбе 3 (рис. 39) сделан соответствующий выступ (стопор) 6.
Перед заливкой баббитом поверхность сегментов тщательно отчищается и облуживается; затем сегменты укладывают в формочку из листового железа, прогревают до температуры 200-250о С и заливают баббитом с достаточным припуском на обработку. Соединение баббитовой заливки с сегментом должно быть безукоризненно плотным, и все сегменты, не удовлетворяющие этому требованию должны быть перезалиты.
Плотность соединения заливки с сегментом может быть проверена следующим способом. Сегменты на несколько часов погружают в горячее турбинное масло, вынимают и насухо вытирают; затем, сильно сжимая пальцами сегмент, осматривают края заливки; если где либо выступит масло, это значит, что заливка выполнен неудовлетворительно.
Входные кромки сегментов подшипника должны быть хорошо закруглены во избежание нарушения масляного слоя. Зазоры между всеми сегментами и гребнем должны иметь одинаковую величину, так как только при этом условии сегменты будут равномерно нагружены; в противном случае возможен не только выход из строя подшипника, но даже поломка вала вследствие усталости, вызванной односторонним давлением.
Необходимую толщину сегментов при отсутствии других данных определяют, измеряя расстояние между упорным гребнем установленного в правильное положение ротора и кольцом . После обработки и шабровки до нужного размера проверяют толщину сегментов посредством индикатора с делениями в 0,01 мм. Для этого сегменты кладут пришабренной поверхностью на проверочную плиту и, проверяя каждый в отдельности индикатором, доводят поодшабриванием до того, чтобы разность в толщине между ними не превышала 0,02 мм.
Затем сегменты устанавливают на место и проверяют по краске равномерность касания упорного гребня, для чего отжимают ротор до упора в сегменты и проворачивают его по направлению нормального вращения. В случае надобности сегменты снова подшабривают. После пробного пуска турбины упорный подшипник должен быть разобран и сегменты вновь осмотрены.
Сегментные упорные подшипники часто комбинируют в одно целое с опорными подшипники, что сокращает длину и уменьшает прогибы вала. На (рис. 45) изображен в разрезе опорно-упорный подшипник, применяемый ЛМЗ для современных конструкций турбин. Вкладыш его благодаря сферической форме опорной поверхности может самоустанавливаться в соответствии с положением вала турбины. Это обеспечивает равномерное распределение нагрузки на сегменты и предупреждает возникновение эксцентрично приложенных к валу осевых усилий, которые в нескольких случаях вызывали поломки валов из-за усталости материала.
Упорные колодки (сегменты) имеются с обеих сторон упорного гребня, так что подшипник может воспринимать усилия, направленные не только вправо, но и влево; последние усилия обычно невелики, поэтому расположенные слева установочные колодки имеют меньшие размеры. К рабочим колодкам масло подводится из камеры 1 по сверлениям в теле вкладыша подшипника. К установочным колодкам оно поступает по трубкам 2. Сливается масло в основном через ряд отверстий 3. Для замера температуры масла установлены два термометра.
Толщина масляной пленки между упорным диском и колодками в сегментном подшипнике достигает значений 0,01 мм и меньше. Поэтому сегменты должны быть пригнаны с большой точностью, и имеется опасность, что при случайном разогревании одного из них и его расширении этот сегмент возьмет на себя всю нагрузку. Для предупреждения аварий по этой причине разработаны конструкции упорных подшипников, у которых нагрузка на сегменты автоматически выравнивается. Если давление на один из сегментов будет больше, чем на остальные, этот сегмент отойдет от упорного гребня, приподнимет соседние сегменты и, уменьшив толщину масляного клина, увеличит давление на них.
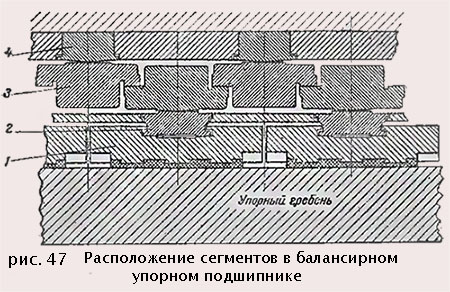
Одной из лучших в этом отношении является конструкция, показанная на (рис. 47). Здесь сегменты 1 опираются на стальные закаленные сухари 2, заключенные в общую обойму. В свою очередь сухари 2 опираются на качающиеся уравновешивающие подушки 3, которые передают осевое давление на неподвижный корпус турбины через стальные каленые сухари 4. Изготовление такого подшипника обходится дороже, чем подшипника обычного типа, но и несущая способность его значительно больше. Поэтому и размеры подшипника получаются небольшими.